In more than 20 years of business, we have manufactured more than 10,000 unique molds. All our die and die-casting equipment are standardized on a global scale, and we coordinate mold resources on a global scale. This means that no matter where your manufacturing location is, we will provide you with support from concept, rapid prototyping, tooling and pre-production testing phases to full production. We offer two types of machining processes: multi-slide and conventional.
Multi-slider die casting mold
We have continuously improved our tools and machines to provide the most advanced die casting process. The multi-slider tool is designed to use four (or more) vertical sliders in the tool, allowing us to create more complex and accurate castings. Multi-slide die casting has many unique advantages, including:
Forming for the first time, eliminating secondary operations such as assembly and processing
Complex geometries and strict tolerances can achieve world-class productivity and reduce overall costs
Compared with standard multi-cavity molds, the difference between parts is minimal
More compact tools, less prone to parting line changes and their negative effects on the dimensional tolerances of finished parts
Conventional die casting mold
Traditional die casting molds have a single cavity (one part per cycle) or multiple cavities (more than one part per cycle). Our conventional processing technology only designs two sliders instead of four sliders, which provides customers with production efficiency and lower costs. When you choose INNOVAW as a die casting company, you will receive:
High-quality molds can effectively deal with mass production
Pay attention to the design of the mold and add many functions of the parts as needed to avoid secondary operations. Our goal is always the first cleansing
Careful planning to eliminate processing and reduce costs
Perform predictive wear analysis to improve the life of the mold. Our tool designers can predict which part of the mold may wear and insert it as a separate steel block
Well-planned water and cooling lines ensure efficient production
Tool design and production
All our tools start with manufacturing design, and we talk with customers to ensure that any defects in parts can be reviewed and corrected before manufacturing tools. Modifying the mold features at the front end will help improve the final part, but it can also improve the overall quality of the tool. In this design stage, we can also predict the wear location of the tool and create a movable blade for the tool to save time and maintenance costs. The tools we designed can run with minimal downtime.
The tool department consists of approximately 25 tool manufacturers, 95% of which have served INNOVAW for more than 15 years. Their knowledge and experience have brought tremendous changes to our customers. Not only are they the best die-casting tools, but they also work with thousands of customers in almost every industry and can modify the solution when any problems arise in the production process.
CAE simulation analysis
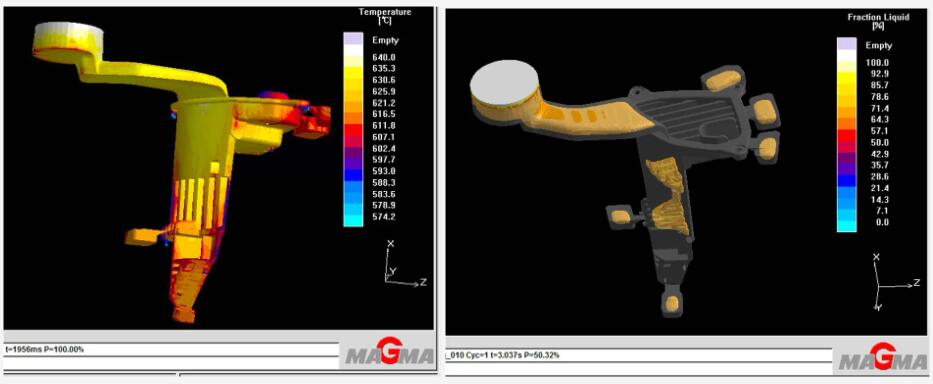
The mold workshop is equipped with a group of professional mold design and manufacturing engineers who are proficient in 2D / 3D computer software to assist in mold design and manufacture machines including CNC machining centers, EDM, WEDM, universal milling machines, friction welding equipment, etc.
Tool design process
INNOVAW has advanced engineering technology and cooperates with customers to design excellent products to achieve cost-effective manufacturing.
At the beginning, in order to meet customer requirements, we will communicate with customers to discuss more details based on the drawings and collect their needs. Then, we use tools such as FEA, mold flow simulation to clarify and identify key unresolved issues that can be resolved to ensure successful production of parts.
In addition, some prototype options also support our product development and tool design process. INNOVAW can provide rapid prototypes and HPDC components within 20 to 35 days-all of which have engineering support to view the results and make necessary recommendations.
Advanced product quality planning process
Product design in CAD/CAM, Pro/Engineer, CATIA or Nx
rapid prototyping
Mold flow analysis
Tool design
Mold procurement and technical review
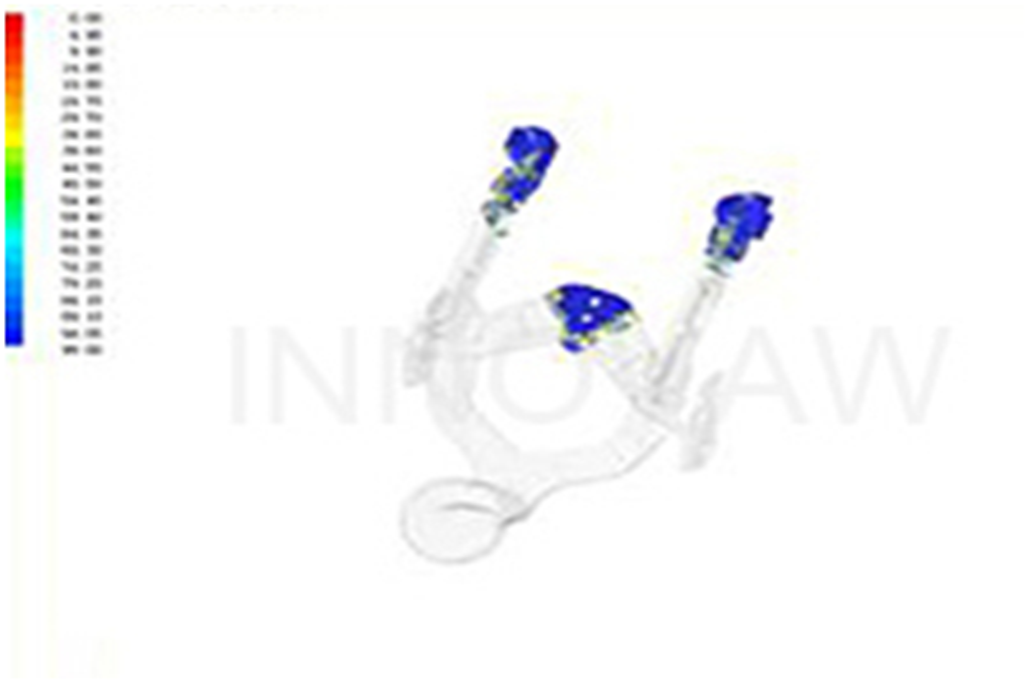
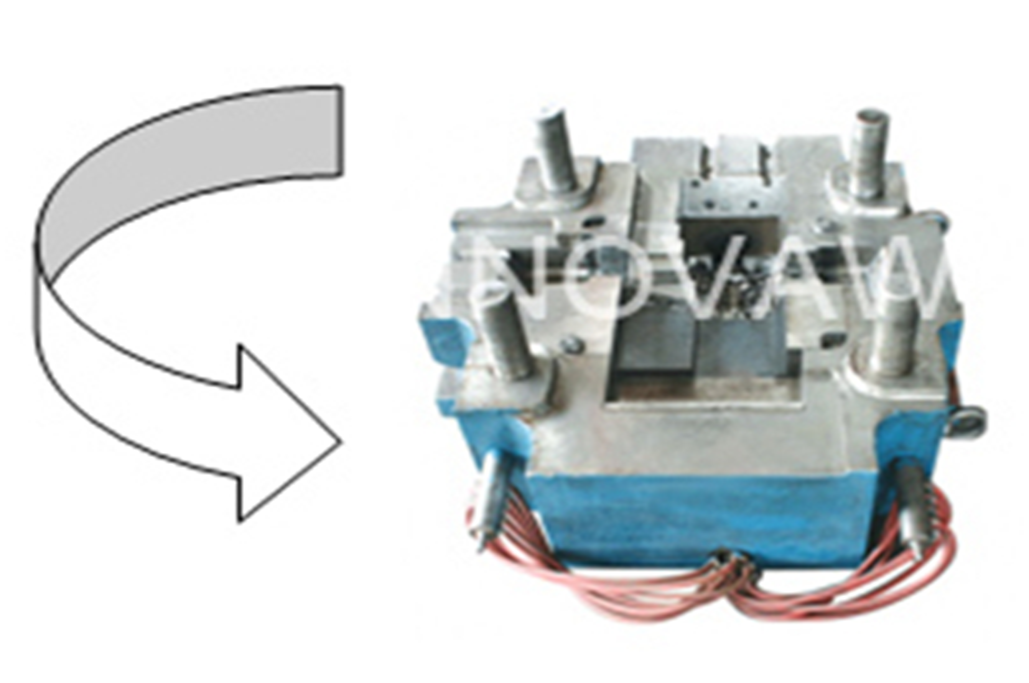
Application Industry
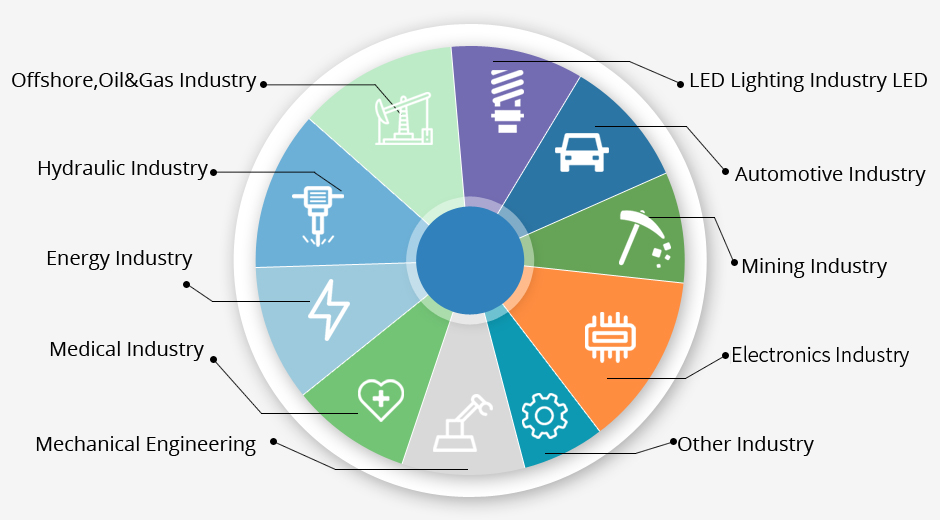
Partner
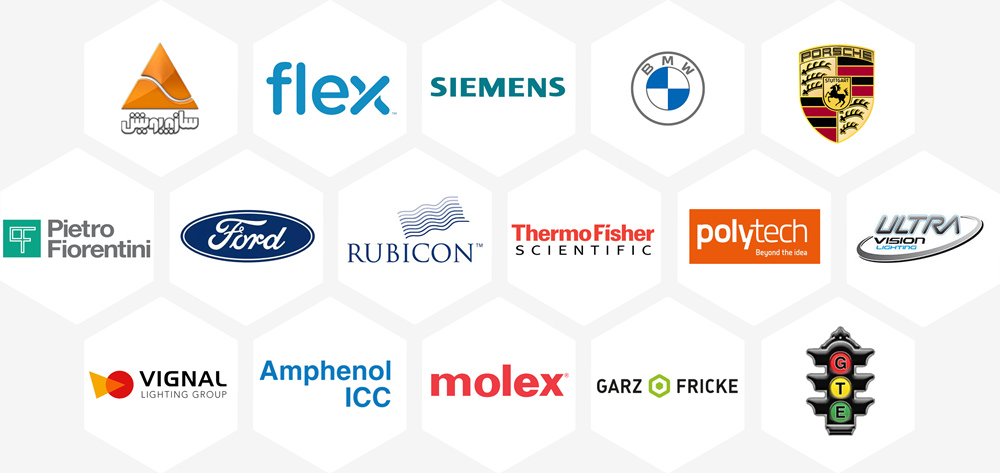